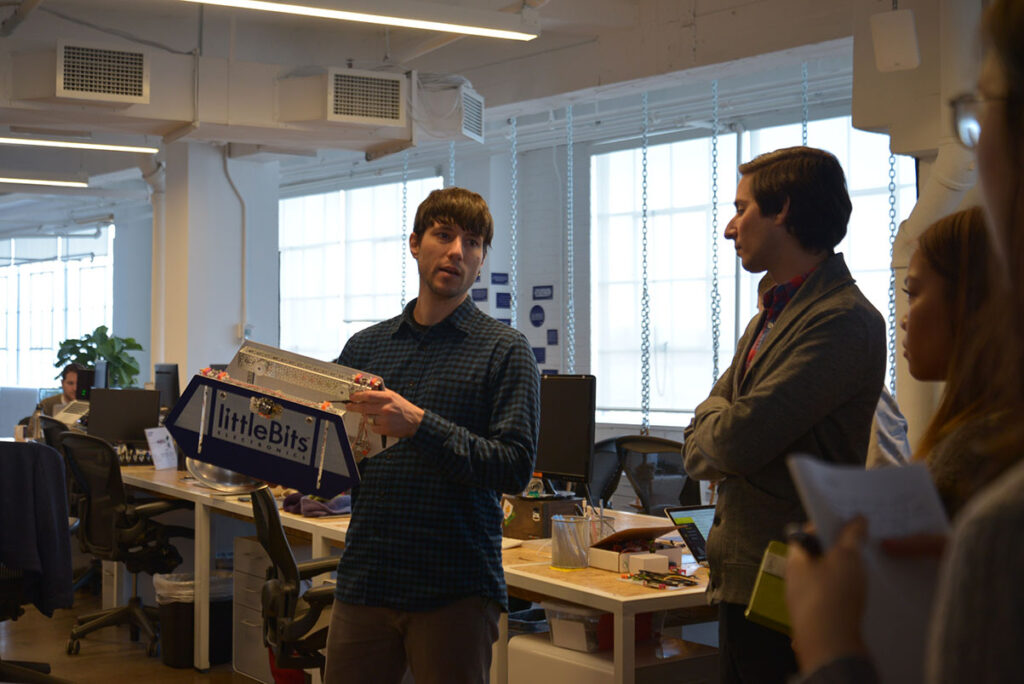
littleBits is the rapid prototyping and high quality educational toy for interaction design. An ambitious variety of electronic modules snap together with colourful magnetic connectors to build robots, musical instruments, toys, home automation devices, and wearables. One notable example, Ringly, a “smart ring” which vibrates and illuminates when you get a notification, raised $5.1 million dollars in funding earlier this year, and was prototyped with littleBits.
What distinguishes littleBits from other construction toys you may be familiar with is that it was built from the ground up for electronic logic. LEGO Mindstorms was an electronics add-on to a primarily structural system. Design choices like magnet polarity, hot swappability of modules, and no need for computer coding also means littleBits is easier to get into than microcontroller platforms like Arduino.
“We try to make products you don’t need to read a manual for.” -Paul Rothman
Our hosts Paul and Jordi lead R&D at littleBits, coming up with new concepts for modules, connections, and other general design work. There are about 56 people working on new modules, their lovely website, marketing, education, and customer support. They gave us a first-class tour of their operations.
The Product
Currently, over 60 different modules represent the littleBits system, some of the most rudimentary being lights, switches, timers, buzzers, motors, filters, oscillators, sensors, etc. Each module’s connector colour is a quick way to determine whether it’s a POWER, INPUT, WIRE (“extend, branch out”), or OUTPUT device.
Paul says although one can purchase individual modules, littleBits hypes the kits because, “You need a certain amount of modules to really get the idea of what you can do with littleBits. If you have 4 or 5 modules–depending on what they are–they may not give you that experience, and then we’re not going to have people coming back and staying in the system.”
As of this posting, average kits cost between $99 and $249 and contain between 6 and 18 modules and some accessories. The One of Everything Collection is $1499, with 112 modules and a smorgasbord of accessories. And finally, the whopping 264-module Pro Library is a $3299 wall-mounted bin storage system designed for “large makerspaces, design agencies, and engineering firms.” You can check it all out on the littleBits store or Amazon.
The modules also have “feet” which allows whatever you’ve snapped together to stand in a mounting board or adhesive “shoes,” and there’s brick adapters for attaching to LEGO.
The Community
What’s really special about littleBits is that it’s not a closed ecosystem. The cloudBit connects your project to the internet, allowing you to wirelessly pull and push data using the IFTTT service.
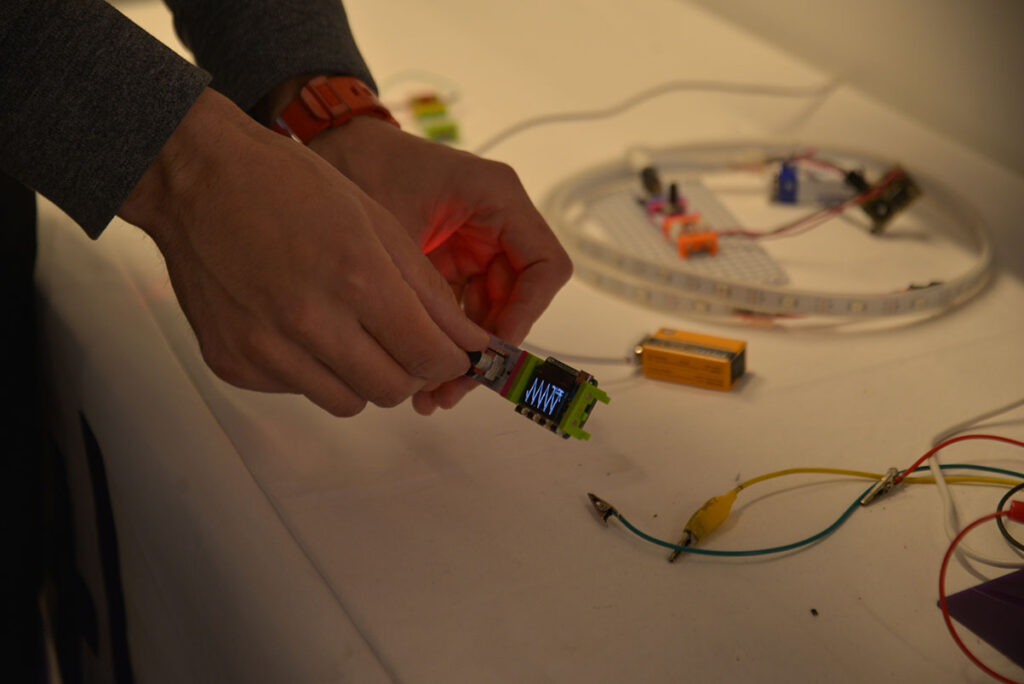
They also launched bitLab last September: module concepts from their community. Tinkerers can use the proto module or the Hardware Development Kit (HDK) to connect standard electronic components to littleBits modules. Proposals with 1000 votes get a review, and if it’s approved for manufacture and sale, the designer gets a 10% royalty. bitLab submission popularity is kinetically visualized near littleBits’ kitchen through a cloudBit-enabled progress bar race. UPDATE: the bitLab is closed as of March 17, 2017.
There is a MIDI module and a control voltage module (for interfacing with analog synths.) There is an Arduno coding kit, which–by extension, allows communication with Processing, MaxMSP, Flash, and other systems; or the USB I/O module connects to your audio workstation software of choice without all the Arduino stuff.
The Facilities
Their classy, inviting headquarters are located in Chelsea, New York, which we accessed through a very “underground mountain lair” hallway painted silver with diamond plate. An open, hardwood floor loft office with purple accents, lots of big windows overlooking the Hudson River, and a comfy lounge utilizes much of the space.
There are littleBits projects on every surface. Jordi shows us a suspended tram robot which reminds me of the Siemens People Mover (SIPEM) system used in Germany and SAFEGE monorail in Japan. There is an LED matrix with a GSM module you can text a message to. A robot hand that plays Rock, Paper, Scissors with you, showcasing Arduino connectivity. There is a synth toaster which was made for an OK GO Pledge Music campaign reward, a cloud-connected fish feeder, a light-powered car, a pinball machine, and an automated curtain.
The rest of their headquarters is divided into a photo/video studio, conference room, some private offices, and an industrial fabrication workshop with power tools and spray booths. There is an electronics lab where they do short runs (20-50 units) of new module prototypes and test them.
Starting littleBits
The littleBits project started in 2008 when founder and CEO Ayah Bdeir was trying to develop a way for electronics to be prototyped quickly and easily, to be able to “sketch” electronics, and build interaction into one’s models.
Working with a grant from Eyebeam and seed round funding in 2011, Sparkfun produced the first 250 kits in Boulder, Colorado. There was Series A round in 2012 and Series B in 2014, working with different VC firms in New York and San Francisco, which allowed them to move into their current headquarters last October.
As Ayah started getting the idea out, the feedback was mostly about education and the toy market. In 2013, they came to the realization that toy market was too cutthroat, full of “cheap crap,” dominated by vested interests. They would have had to dumb down their refined, high-quality product. “Trying to make a product hit a price point doesn’t always work because the experience of using that product is not good enough,” says Paul.
Staying Young & Connected
As more established companies are realizing the value of startups by snapping them up or even starting their own, how does a developing company like littleBits maintain the youthful vibrance so essential to its identity and products?
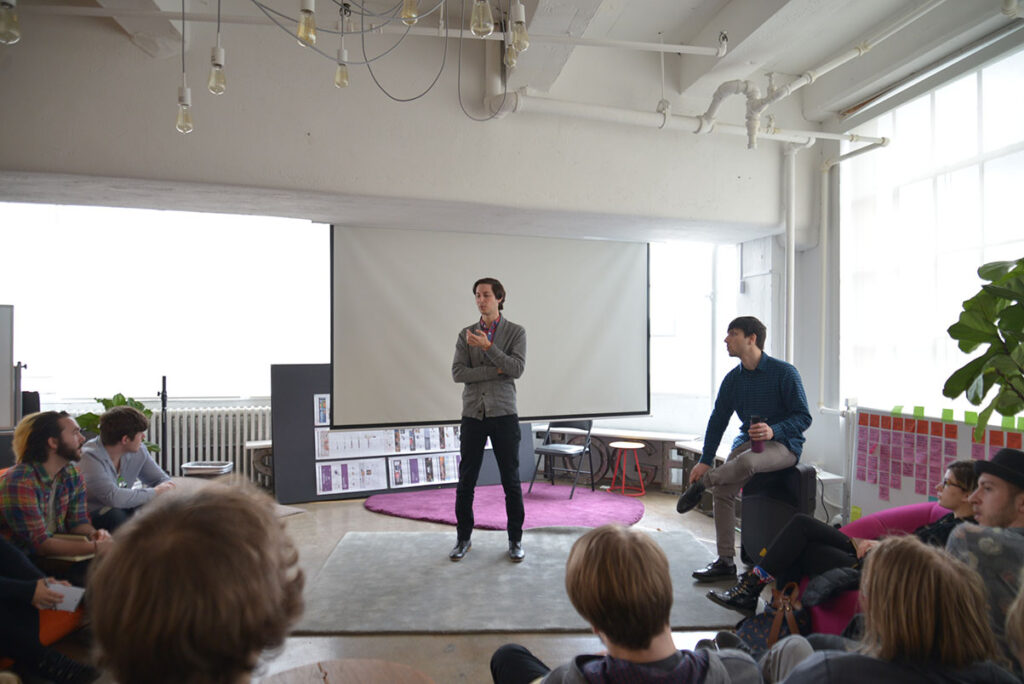
Paul says maintaining the startup family culture is a very conscious thing. “We have team meetings every Tuesday in our lounge, hire people with good emotional and group skills, spend time outside the office together, and eat together.” He says it’s also important that new hires don’t fly under the radar, “Because it’s no longer four of us in a 10’ x 10’ coworking space. There were no meetings back then. You just turned and talked to the person.”
For communication tools, the team used Basecamp in the beginning, but now it’s mostly Gmail + Hangouts, Trello, Slack, Google Docs, and Dropbox.
Iterative Design
Glass cases near the entrance are a development timeline, containing the cardboard prototype Paul put together in 2008, some of the first PCBs, plastic injection molding with magnets and pins, receipts from first sale in 2011, laser cut prototypes of the packaging, and a science kit developed with NASA.
After their first production run, they decided the plastics company that was making the module connectors wasn’t doing a very good job. Switching to a precision connector company, AUK Contractors solved this problem. Jordi tells us how they didn’t want to leave anyone behind, so they made sure their original customers got foam spacers for backwards compatibility. Entrepreneurs, take note. This is how you treat your champions.
The weekly Customer Service Report is taken very seriously: pain points, frustrations with products, favourite things, and problems that prompt module redesigns. For example, the motor module was redesigned based on customer feedback so its direction could be reversed dynamically without needing to flip a switch on it.
Six months is a very fast pace to develop simple modules because a lot of time is spent ensuring complex interaction possibilities and intuitiveness. Sometimes the inspiration starts with the technology. “If we were to use RFID, what does that unlock?,” Paul muses, “An electronic boardgame, or effects triggered by people moving through a space?” Other times it’s an desired interaction in search of technology.
littleBits KORG Synth Kit
I was very interested in the KORG-branded Synth Kit, and how partnerships like this are weighted. It started with an interested email from KORG, where they connected on the idea of a modular synthesizer. Paul’s background is in audio.
Paul says KORG is an unusually forward-thinking company for having been around for 50+ years, and has adapted to the explosion of amateur music production by making smaller, cheaper products. Product lines like the $400 MicroKORG and $50 Monotron is stuff synth competitors like Roland or YAMAHA aren’t doing (YAMAHA actually owned a controlling stake KORG in 1987, but functionally, founder Tsutomu Katoh maintained full autonomy over the successful company and was able to buy most of it back in 1993.)
KORG provided know-how and their name for the product in return for royalties. They also sell littleBits in their stores, and are the exclusive distributor in Japan. It took some negotiation, but KORG eventually agreed to open sourcing the designs.
Development of the 12 modules in the KORG synth kit took nine months from concept to shipping. I haven’t tried it, but it looks super fun. Prepare for bewilderment.
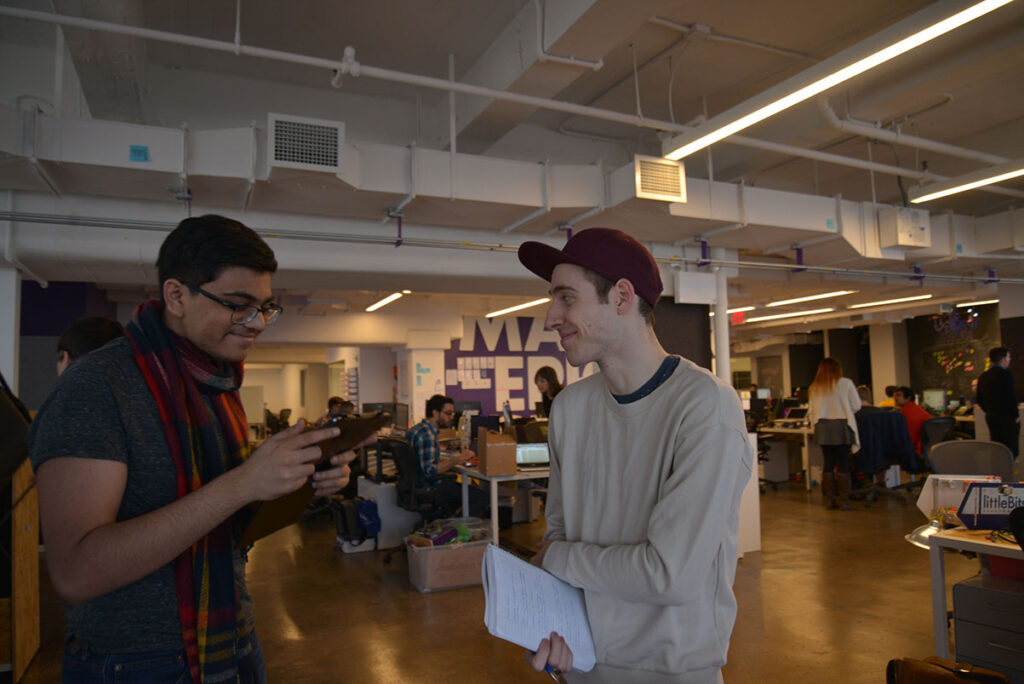
Besides new modules, they are investigating ways to make the platform more physically flexible for wearables. While littleBits is still gaining traction with design professionals, they would also like to see advertising agencies get some. Paul says, “It’s a way to train creatives into thinking of technology as a part of design, not something separate, added later.”
Lee Saynor is a Digital Futures undergrad at OCAD University. The keystone of Atelier II – Collaboration was a week-long field trip in New York City, where the class visited some of the most important people and organizations in creative technology. Thank You Paul & Jordi!
NOTE: This post was edited on March 17, 2017 to update links and the paragraph on the bitLab pilot project.
Leave a Reply